How to Control the Quality of Asphalt Plant Output?
- Share
- Issue Time
- Aug 13,2021
Summary
Put it simply, asphalt is like glue, and it uses bitumen, an oil-based substance, to make sand and crushed rock stick to each other together. As a kind of commonly used road surface paving material, asphalt plays a vital part. It can be said that a roadway with a substandard blacktop material will fail prematurely. There are 7 aspects from which asphalt quality control starts.
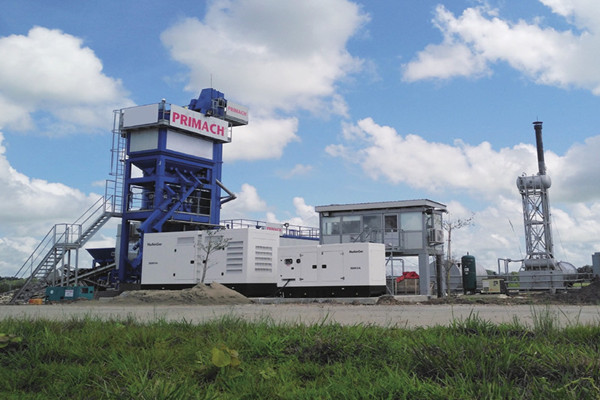
Put it simply, asphalt is like glue, and it uses bitumen, an oil-based substance, to make sand and crushed rock stick to each other together. As a kind of commonly used road surface paving material, asphalt plays a vital part. It can be said that a roadway with a substandard blacktop material will fail prematurely. There are 7 aspects from which asphalt quality control starts.
1. Coarse Aggregate
Coarse aggregates are cube particles with rough surfaces and corners, and their particle size varies from 2.36mm to 25mm. To produce high-quality asphalt mixture, the content of sheet-like particles must be low, so that the interlocking effect of the particles can provide stability and resist displacement through friction.
2. Fine Aggregate
Fine aggregate refers to gravel with a particle size between 0.075 and 2.36 mm. When used as an ingredient to produce asphalt, it must be clean and free of clay and other harmful substances. It also should have some edges and corners to increase the interlocking effect between the particles and reduce the pores between the aggregates and ultimately increase the stability of the mixture.
3. Bitumen
Bitumen should be selected according to the local climate. The higher the grade of bitumen, the greater the penetration and the lower the consistency. It is suitable for areas with lower temperatures and the road surface has better low-temperature crack resistance but poor high-temperature stability. The higher the consistency of the bitumen, the higher the penetration PI index, and the higher the high temperature stability and rutting resistance of the pavement, but the poor thermal crack resistance.
4. Mixing Ratio Control
The design of the mixing ratio should be selected from repeated tests. After the quantity of each ingredient is determined, a Marshall test should be carried out to determine the optimal bitumen dosage, and thereby determine the proportion of other ingredients.
5. Temperature Control
Bitumen heating is controlled at 150~170℃. The temperature of mineral material is 10~20℃ higher than bitumen. The factory temperature of the final mixture is 140~155℃. When transported to the paver, the temperature is controlled between 135~150℃. The compaction temperature should not be lower than 135℃, the final compaction temperature should not be lower than 110℃, and the open traffic should not be higher than 60℃.
6. Oil-stone Ratio Control
The oil-stone ratio is the ratio of the quality of bitumen in asphalt concrete to the mass of additives such as sand. It is the most important indicator for controlling asphalt concrete. If the oil-stone ratio is too large, "oil cake" will appear after paving and rolling. If the ratio of oil stone is too small, the pavement material will diverge and it will not be formed by rolling.
7. Mixing
It is required that all particles are wrapped by the bitumen, without uneven packaging, no agglomeration or serious segregation, and the mixture that is found to be charred, carbonized, foamed and water-containing must be discarded.
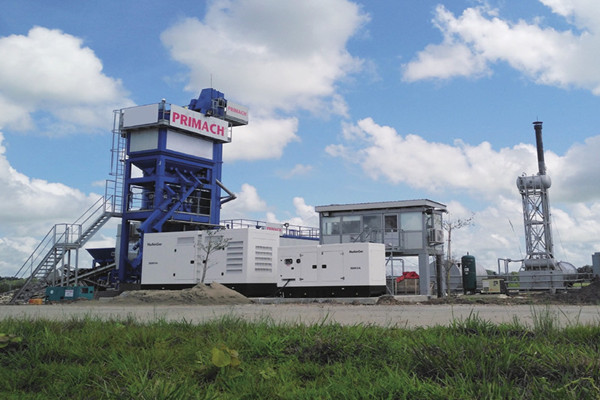