CONTINUOUS DRUM MIXING PLANTS
- Share
- Issue Time
- Oct 28,2020
Summary
The single most important factor affecting the production rate of a particular size of continuous drum plant is the moisture content of the aggregate entering the dryer drum.
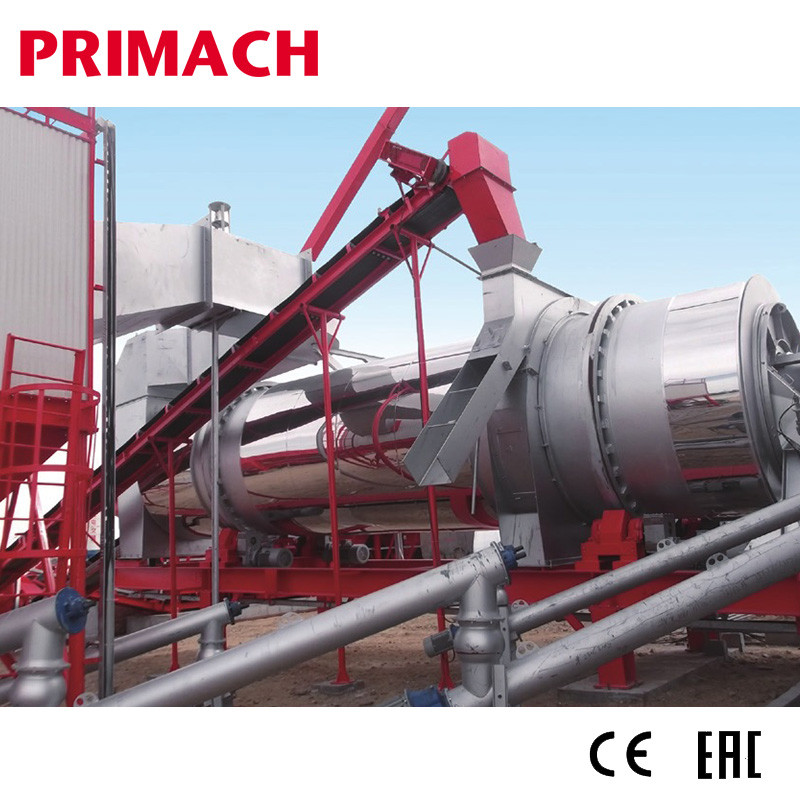
Continuous mixing in drum plants differs from batch plants in that the aggregate is dried, heated and mixed with the binder in the one operation, eliminating the need for:
● hot elevator
● vibrating screens
● hot aggregate storage bins
● weigh hopper
● pugmill.
In the most common form of drum mixer, described in this section, a conventional type burner (either oil or gas) is located at the aggregate inlet end of the drum and hot bitumen is added part way along the drum. This is also termed parallel flow.
Other forms of drum mixing plant, including counterflow of aggregates and heating, separate chambers for heating and mixing, and alternative heating systems are also used, particularly for the
manufacture of recycled mixes as described in Section 6.
The capacity of a drum mixer, in tonnes per hour, depends primarily on the drum size, but effective production rate is also influenced by burner size and moisture content of the aggregate.The single most important factor affecting the production rate of a particular size of continuous drum plant is the moisture content of the aggregate entering the dryer drum.